Injection Molding Factories: Transforming Metal Fabrication for a Sustainable Future
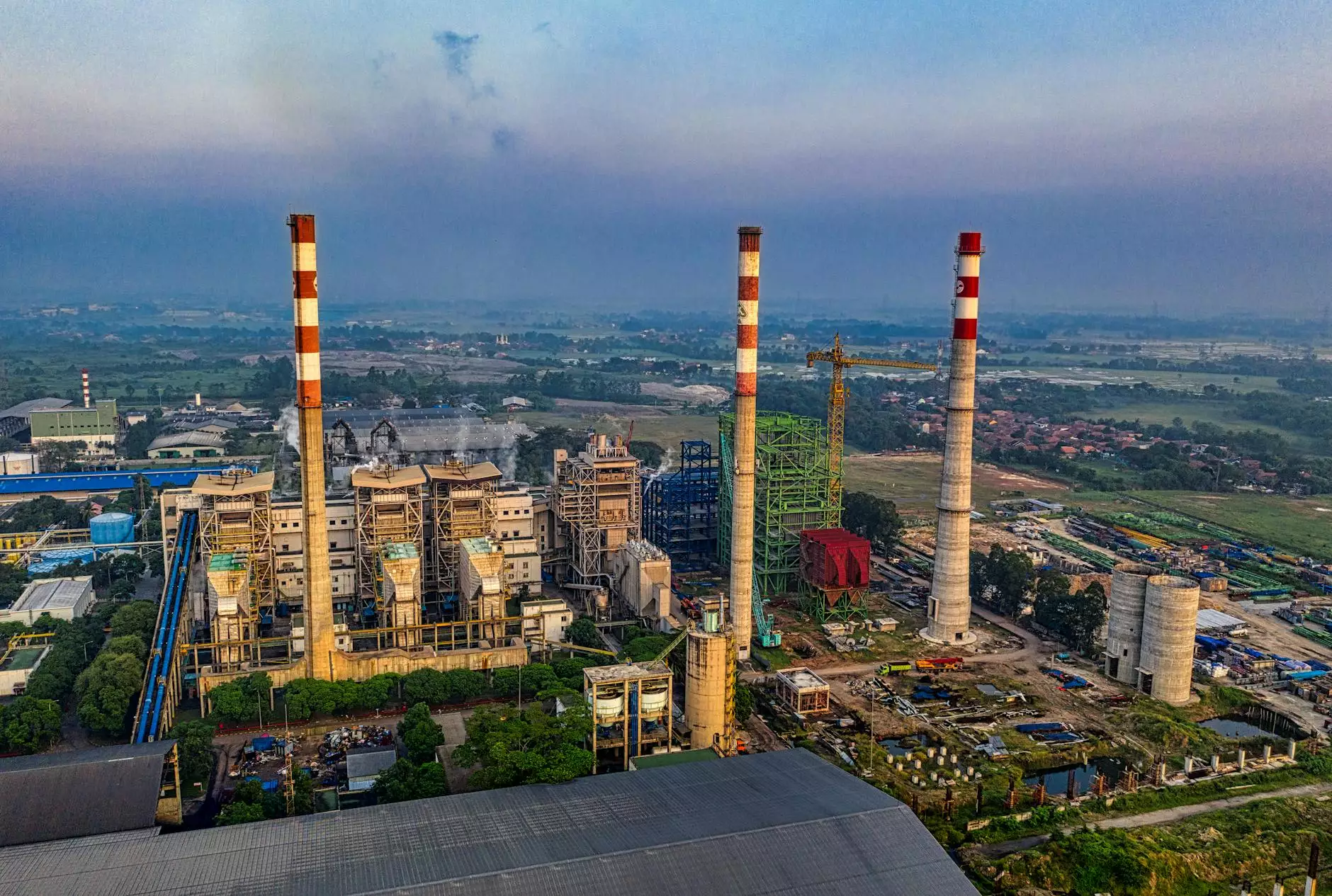
In today's rapidly evolving industrial landscape, injection molding factories play a crucial role in advancing the manufacturing process, particularly in the realm of metal fabricators. This article delves deep into the intricacies of injection molding, discussing how these factories operate and their significance in modern business operations.
Understanding Injection Molding
Injection molding is a manufacturing process used to produce parts by injecting molten material into a mold. This technique is widely utilized for creating parts made from various materials, including plastics, metals, ceramics, and even composite materials. The process is highly efficient, allowing for rapid production of complex shapes with excellent precision.
How Injection Molding Works
The injection molding process involves several key steps:
- Material Preparation: Raw material, typically in granule form, is fed into a heated barrel.
- Injection: The material is heated until it becomes molten and is then injected into the mold under high pressure.
- Cooling: The molten material cools and solidifies within the mold, taking its shape.
- Demolding: Once cooled, the mold opens, and the finished part is ejected.
- Finishing: Additional processes, such as trimming or machining, may be applied to refine the final product.
The Role of Injection Molding Factories in Metal Fabrication
Injection molding factories have become essential players in the metal fabrication sector. By leveraging the advantages of injection molding, these factories can create high-quality metal components that are integral to a wide array of applications, including automotive, aerospace, household goods, and more.
Advantages of Injection Molding in Metal Fabrication
Utilizing injection molding in metal fabrication offers numerous benefits:
- Efficiency: Injection molding is a highly automated process, minimizing labor costs and reducing production times.
- Precision: Components manufactured via injection molding have tight tolerances, ensuring consistent quality.
- Material Utilization: The process generates minimal waste, making it an environmentally friendly manufacturing option.
- Versatility: Injection molding can be used to produce a wide variety of part shapes and sizes.
- Scalability: Once the mold is created, producing additional units becomes increasingly cost-effective.
Applications of Injection Molding Factories
Injection molding factories cater to numerous industries, producing parts that are both functional and aesthetic. Some prevalent applications include:
1. Automotive Industry
The automotive sector is one of the largest consumers of injection-molded parts. Components such as:
- Dashboard panels
- Exterior trim
- Battery housings
are commonly produced using injection molding due to the process's ability to create lightweight yet robust parts.
2. Consumer Electronics
Injection molding allows for the rapid production of components used in consumer electronics, including:
- Smartphone cases
- Remote controls
- Computer housings
3. Medical Devices
The stringent quality control requirements of the medical industry are met through injection molding technology, allowing for the production of:
- Syringes
- Implants
- Diagnostic equipment housings
Technological Advancements in Injection Molding
The evolution of technology has led to significant advancements in injection molding processes. Some exciting developments include:
1. 3D Printing Integration
Utilizing 3D printing to create molds has increased design flexibility and reduced lead times for injection molding.
2. Advanced Materials
The introduction of engineering thermoplastics and other innovative materials enhances performance characteristics, such as temperature resistance and mechanical strength.
3. Smart Manufacturing
Incorporating IoT devices into the molding process allows for real-time monitoring and adjustments, leading to improved efficiency and reduced downtime.
Challenges Faced by Injection Molding Factories
Despite their advantages, injection molding factories confront several challenges, including:
- High Initial Costs: The costs associated with developing molds can be substantial, making the initial investment significant.
- Material Limitations: Not all metals are conducive to injection molding, limiting material options.
- Skill Gap: Finding skilled workers with the necessary expertise in modern injection molding techniques can pose an issue for some factories.
Future Trends in Injection Molding Factories
The landscape of injection molding is continually evolving, and several trends are likely to shape the future of injection molding factories:
1. Sustainable Practices
As industries aim for sustainability, injection molding factories are adopting environmentally friendly practices, such as using recycled materials and minimizing energy consumption.
2. Customization and Personalization
With the rise of personalized products, injection molding is expected to adapt to producing smaller runs of customized parts efficiently.
3. Automation and Robotics
The integration of automation and robotics in injection molding processes enhances throughput and quality assurance, moving towards a fully automated manufacturing environment.
Conclusion: The Future of Injection Molding Factories in Metal Fabrication
The significance of injection molding factories in modern metal fabrication cannot be overstated. As they continue to innovate and adapt to the evolving industrial landscape, these factories are set to play a pivotal role in ensuring efficiency, quality, and sustainability in manufacturing. By embracing new technologies and practices, the future of injection molding in metal fabrication looks promising, paving the way for a more sustainable and efficient industrial environment.