Understanding PC ABS: A Versatile Material for 3D Printing
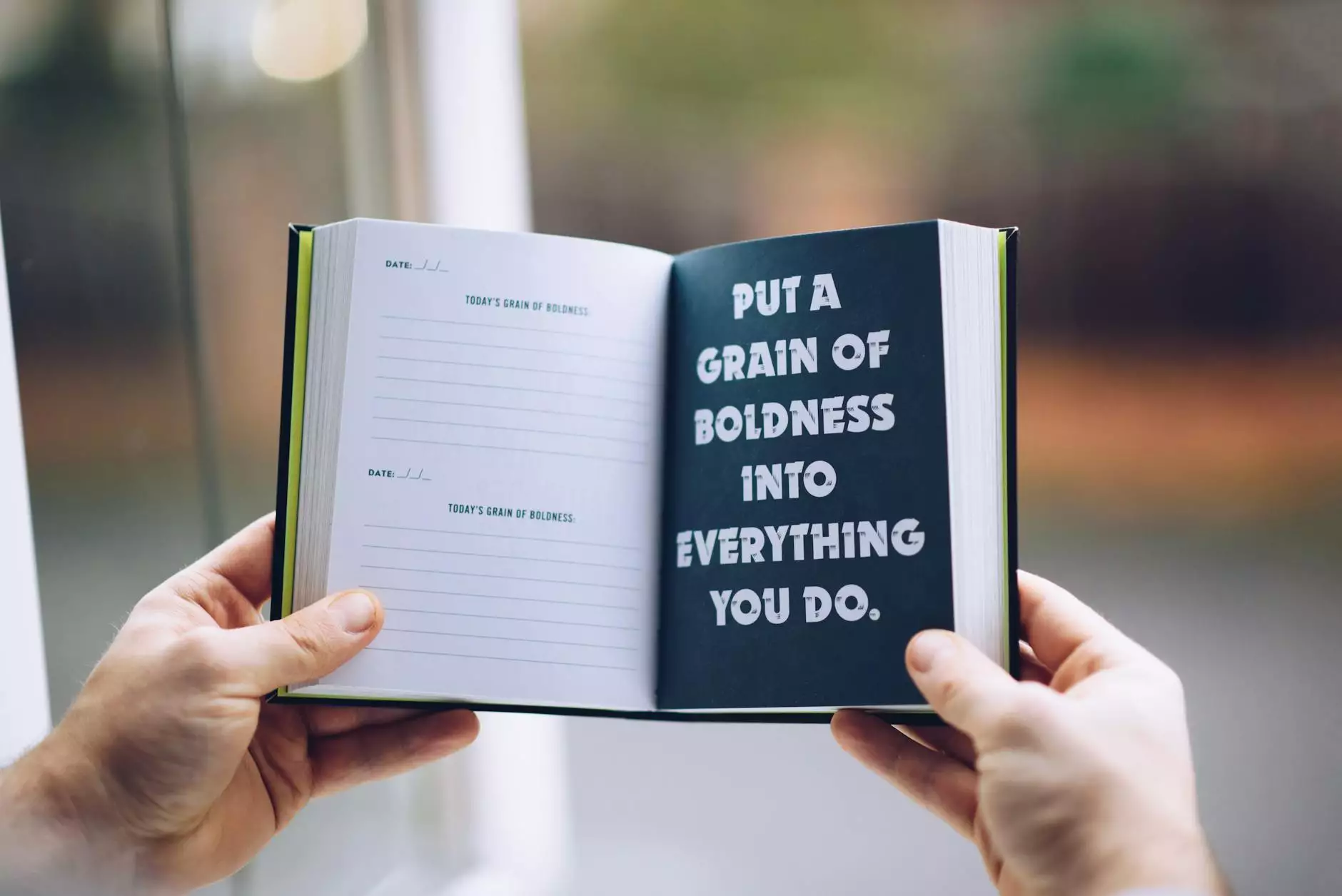
PC ABS is an abbreviation for Polycarbonate Acrylonitrile Butadiene Styrene, a remarkable thermoplastic that has gained immense popularity in the realm of 3D printing. The unique properties of PC ABS make it an ideal choice for a variety of applications, ranging from prototyping to final products. In this comprehensive article, we will delve into the characteristics, advantages, and applications of PC ABS, highlighting why it stands out in the 3D printing industry.
What is PC ABS?
PC ABS is a blend of two powerful polymers: polycarbonate (PC) and acrylonitrile butadiene styrene (ABS). Polycarbonate is known for its durability and heat resistance, while ABS is prized for its flexibility and ease of use. This combination results in a material that offers the best of both worlds: the strength and toughness of polycarbonate, along with the processing advantages of ABS.
Key Characteristics of PC ABS
- High Impact Resistance: One of the most notable features of PC ABS is its exceptional toughness. This makes it suitable for applications that require durability.
- Temperature Resistance: PC ABS can withstand elevated temperatures, making it an excellent choice for parts exposed to heat.
- Good Chemical Resistance: It has a robust resistance to chemicals, which extends its usability in various industrial applications.
- Excellent Surface Finish: The material provides a smooth finish, reducing the need for extensive post-processing.
- Versatile Printing Options: PC ABS is compatible with many 3D printers and can be easily processed in various ways.
Applications of PC ABS in 3D Printing
The versatility of PC ABS enables its use across a broad spectrum of industries. Here are some of the prominent applications:
1. Prototyping
PC ABS is extensively utilized for rapid prototyping, allowing engineers and designers to create durable and functional prototypes that can withstand testing and evaluation processes. This capability accelerates product development timelines significantly.
2. Automotive Industry
In the automotive sector, PC ABS is favored for making interior components, including dashboards, trims, and housings. Its high impact resistance and ability to be colored easily contribute to both aesthetics and safety in vehicle design.
3. Electronics Housing
With its effective insulation and thermal resistance properties, PC ABS is ideal for producing housings for electronic devices. From smartphones to complex machinery, this material enhances performance and durability.
4. Medical Devices
The medical industry benefits from PC ABS due to its biocompatibility and ability to generate precise, sturdy components. This includes frameworks for medical devices, tools, and instrument housings that need to meet rigorous safety standards.
Benefits of Using PC ABS in Your Projects
Choosing PC ABS for your 3D printing projects carries numerous advantages:
- Cost Efficiency: The blend of properties translates to fewer iterations and less waste, leading to cost savings in development.
- Enhanced Durability: Projects stand the test of time, maintaining quality and performance even under harsh conditions.
- Customization: PC ABS is easily customizable, allowing for color changes and modifications to fit specific project requirements.
- Ease of Use: Its compatibility with a range of printers and ease of handling make it an excellent choice for both professionals and hobbyists.
3D Printing with PC ABS: Tips and Best Practices
For the best results when printing with PC ABS, consider the following tips:
1. Choose the Right Printer
Ensure your 3D printer can handle high-temperature filaments. Industrial or high-end consumer printers are recommended for PC ABS due to their capability to maintain necessary temperatures.
2. Maintain Proper Temperature
Melt temperatures for PC ABS generally range between 230°C to 260°C. Managing print temperatures properly can enhance adhesion and reduce warping.
3. Use a Heated Bed
A heated print bed is crucial for preventing warping and ensuring layer adhesion. Setting it to around 80°C typically yields the best results.
4. Optimal Cooling Settings
While cooling is essential, excessive cooling can lead to warping. Gradual cooling strategies should be used to allow layers to bond properly as the print progresses.
Common Challenges When Printing with PC ABS
Although PC ABS has many advantages, it is essential to be aware of potential challenges:
1. Warping
Due to the nature of PC ABS, warping can occur if temperature settings fluctuate. Ensuring a stable environment can mitigate this issue.
2. Adhesion Issues
Parts may have trouble adhering to the print bed. Utilizing an adhesive solution or a specialized bed surface can help with this problem.
Conclusion: Elevate Your 3D Printing Projects with PC ABS
In conclusion, PC ABS represents a formidable material option for various 3D printing applications. Its blend of durability, temperature resistance, and processing ease makes it an outstanding choice for engineers, designers, and businesses alike. By incorporating PC ABS into your projects, you not only enhance your production capabilities but also ensure that your final products stand out in quality and performance.
To learn more about how PC ABS can transform your 3D printing outcomes or to explore our other offerings, visit us at Infotron.