The Ultimate Guide to High Pressure Die Casting Mould
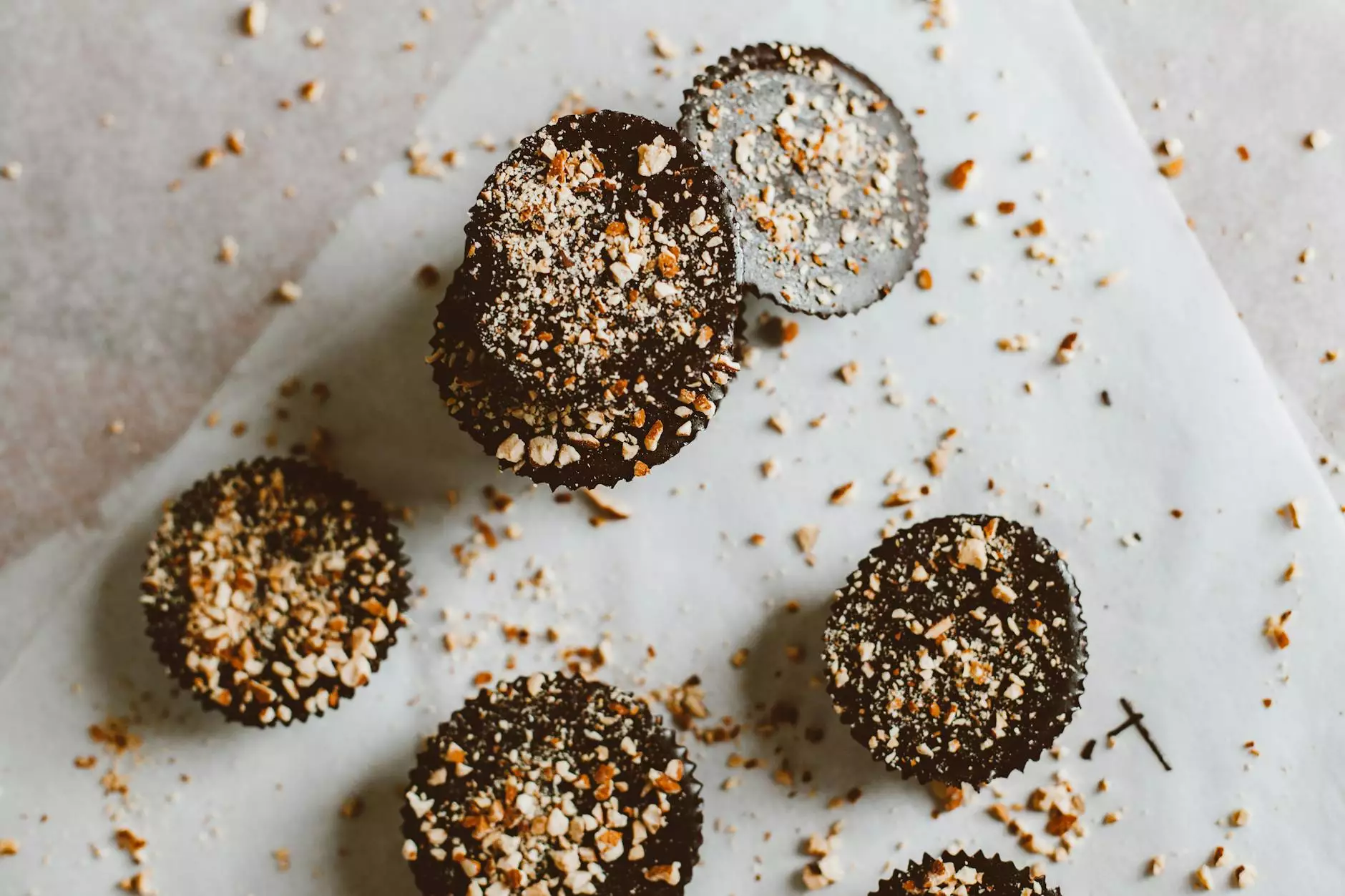
Introduction to High Pressure Die Casting Mould
High pressure die casting moulds are integral to the manufacturing sector, particularly within the metal fabrication landscape. This process allows for the production of complex parts with excellent surface finish and dimensional accuracy. As industries seek more efficient and precise manufacturing methods, understanding high pressure die casting is key to staying competitive.
What is High Pressure Die Casting?
High pressure die casting is a versatile manufacturing process that involves the injection of molten metal into a precisely designed mould under high pressure. This technique is particularly used for non-ferrous metals such as aluminum, zinc, and magnesium. The process can produce numerous components with intricate designs, delivering superior strength and lightweight properties.
Advantages of High Pressure Die Casting Moulds
High pressure die casting moulds offer several advantages that make them a preferred choice in many industries. These advantages include:
- High Precision: The process allows for the creation of intricate shapes with tight tolerances.
- Improved Surface Finish: Parts produced have a smooth surface, which often requires little to no secondary finishing.
- Efficiency: The rapid cycles of die casting lead to high productivity and lower costs per unit in mass production.
- Material Utilization: It minimizes waste, thereby increasing the efficiency of material usage.
- Versatility: Applicable to a wide range of shapes and sizes across various industries.
The Process of High Pressure Die Casting
1. Preparation of the Die
The first step involves the creation of the die, which is typically made from hardened steel or other high-strength materials. The design must accommodate the thermal expansion of the metal and facilitate ease of part ejection.
2. Melting the Metal
Next, the base metal is melted in a furnace. The temperature must be precisely controlled to ensure optimal flow properties for the casting process.
3. Injection into the Die
Once melted, the molten metal is injected into the die at high speeds (up to 120 m/s). This high pressure ensures that the metal fills all cavities and contours of the mould quickly, preventing premature solidification.
4. Cooling and Solidification
After injection, the metal cools and solidifies within the die. Cooling times can vary depending on the thickness of the part and the material used.
5. Ejection of the Part
Once solidified, the mould opens and the newly formed part is ejected. The die is then prepared for the next cycle.
Applications of High Pressure Die Casting Moulds
High pressure die casting moulds are widely used across various sectors, including:
- Automotive Industry: Components such as engine blocks, transmission cases, and housings.
- Aerospace: Lightweight and complex structural components.
- Electronics: Housings for devices, connectors, and structural frames.
- Consumer Goods: Parts for various household appliances and tools.
- Medical Devices: Precision parts for diagnostic and therapeutic equipment.
Choosing the Right High Pressure Die Casting Mould Manufacturer
When selecting a manufacturer for high pressure die casting moulds, consider the following factors:
- Experience: Look for manufacturers with a proven track record in die casting.
- Technology: Advanced machinery and technology can greatly enhance the quality and precision of the mould.
- Material Quality: Ensure that the manufacturer uses high-quality materials for durable and precise moulds.
- Customer Support: Effective communication and support during the process are crucial for ensuring that your specifications are met.
- Timely Delivery: Ensure the manufacturer commits to and adheres to timelines for the delivery of moulds.
Future Trends in High Pressure Die Casting Technology
The future of high pressure die casting is bright, with several trends shaping its evolution:
- Increased Automation: Integrating robotics into the die casting process can enhance efficiency and precision.
- Use of Advanced Materials: Research into new alloys and composites may lead to better performance and sustainability.
- Enhanced Sustainability: Focus on reducing waste and improving energy efficiency throughout the die casting process.
- 3D Printing Integration: The potential application of 3D printing for tooling and parts might revolutionize the industry.
- Diversity in Applications: Expanding applications in electric vehicles and renewable energy sectors.
Conclusion
Understanding high pressure die casting moulds is essential for industries focused on efficiency, quality, and precision. With their numerous advantages and applications, they represent one of the most effective methodologies in modern manufacturing. By staying informed about technological advancements and choosing the right partners, businesses can leverage these processes to gain a competitive edge in the market. To explore more about high pressure die casting mould solutions, visit Deep Mould and discover how our expertise in metal fabricators can meet your needs.